Podcast 8
Ask the Builder Podcast 8 Highlights:
- Karen's wondering if she needs a new paver or blacktop drive. Tim has a better idea.
- Brian needs some tips about painting the inside of a concrete block building
- Lauren wonders about attic framing lumber, a slanted floor and some cracks in her home
- Tim shares a funny story about the first time he had to redo a project. NOTE: Transcript of this story below.
- You can read another true funny story about the coefficient of continuity if you want!
Podcast Sponsor: Stain Solver - Certified Organic Oxygen Bleach
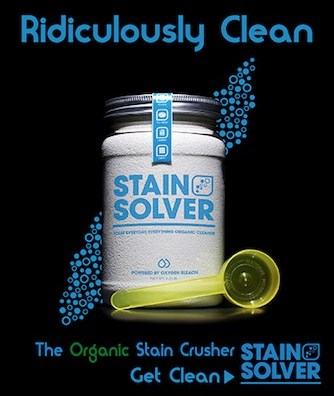
Stain Solver is MADE in the USA with USA ingredients that are food-grade quality. CLICK THE IMAGE to order some NOW.
Home Improvement and Home Construction Podcast
Photos, Links and Great Stuff:
Podcast Opening Videos:
New 3-Way Switch Troubleshooting Video - Pretty Funny Ending!
CALL 1 Karen's Blacktop Drive Repair:
During the call with Karen, I suggested to her that she use the following epoxy you see me use in the following video. Read the columns BELOW the video to understand the process of embedding the stones and sand in the fresh epoxy to completely disguise it:
Related Links:
Blacktop Crack Repair Using Black Goo in Caulk Tubes
Blacktop Crack Repair Using Epoxy and Stones - THIS IS THE ONE TIM RECOMMENDED TO KAREN
Call 2 - Brian's Concrete Block Paint Job
Related Links:
Lead Paint Test Kits - CLICK TO PURCHASE
Call 3: Lauren's Old Timbers:
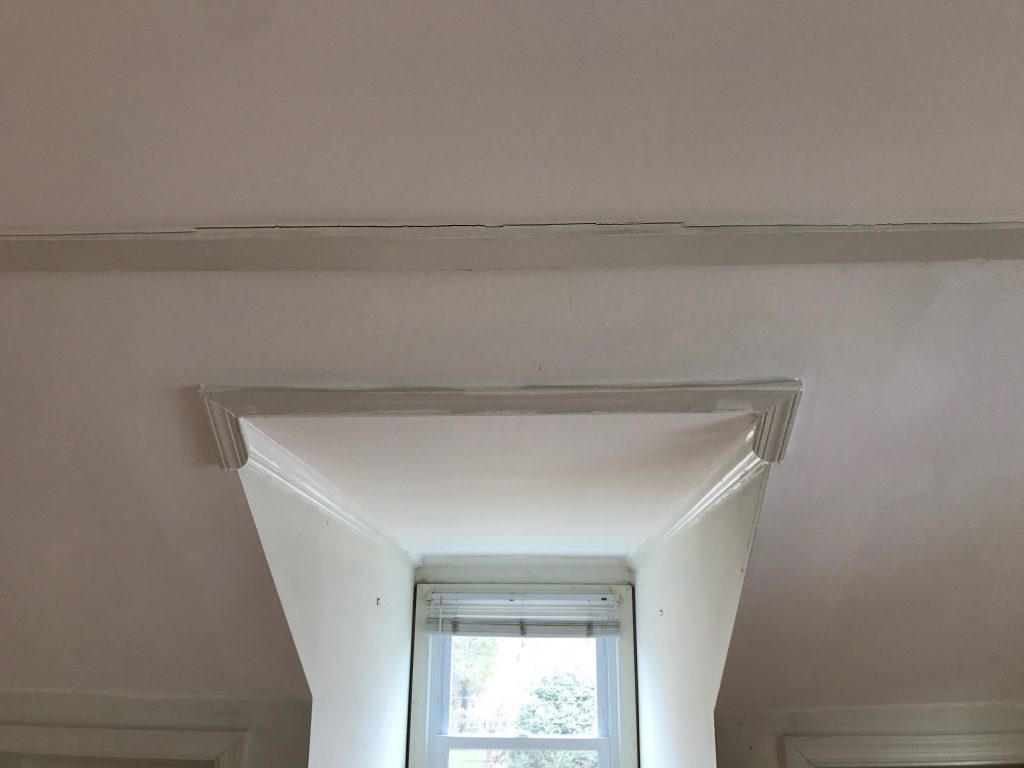
Here are some of the cracks Lauren was talking about. Copyright 2018 Tim Carter
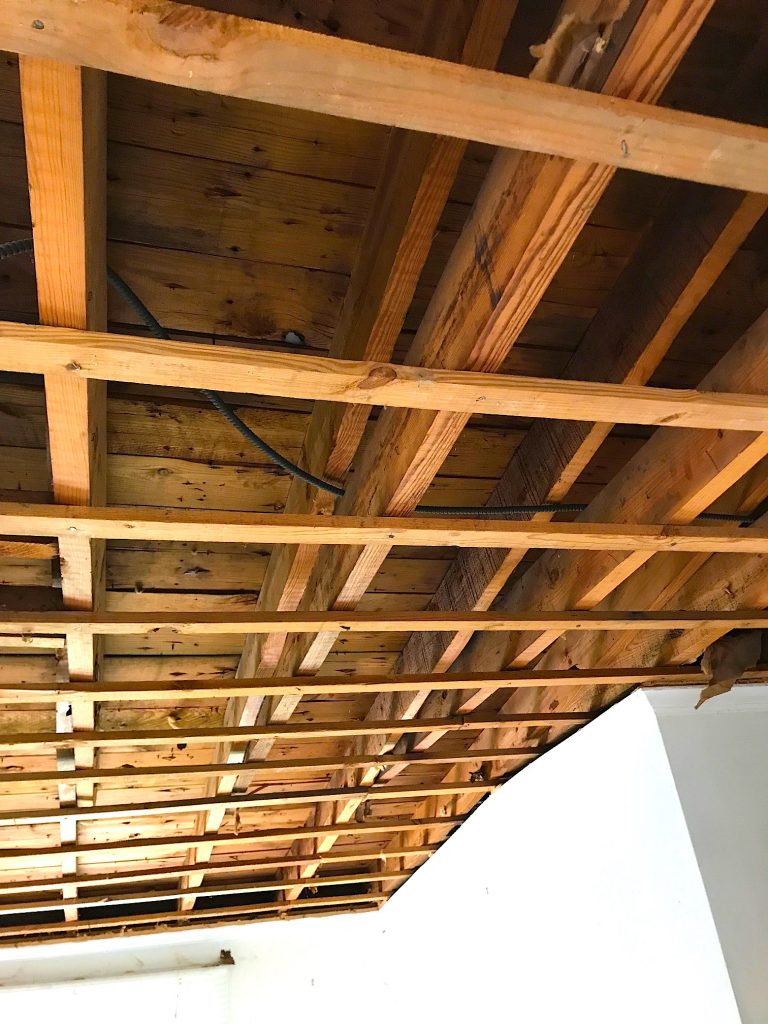
This old timber is in great shape. I wish I could build a new home with lumber like this. Copyright 2018 Tim Carter
Origin of the Do It Right, Not Over AsktheBuilder Motto Story
As Kathy and I approached our second wedding anniversary, we already had purchased, remodeled and sold our first home. Our second home was an older giant five-bedroom home at 6270 Robison Road in the Pleasant Ridge community in Cincinnati, Ohio.
A nice older woman owned the home and it was in very good condition for the most part. One of the things Kathy wanted to change was the front sidewalk. It was an ancient concrete sidewalk poured in a unique way. Many old homes in Cincinnati had what I came to call Clinker Concrete.
The top of the sidewalk was a mixture of very coarse sand and Portland cement. Usually, it was about one and one-half to two-inches thick. This slurry was poured over a base of compacted interlocking coal-furnace clinkers. The entire thickness of the concrete was usually about 4 to 5 inches.
Believe it or not, it made for a durable pavement for foot traffic. The thinner sand-mix concrete didn’t hold up well if you tried to do the same thing for a driveway, although quite a few people did try this.
The old sidewalk extended in a straight line from the front door out to the city sidewalk. My guess is this was the thing to do when neighbors came to visit using their foot mobiles. There was a side set of steps off the full-width front porch in case you needed to get to the front door from the driveway.
Kathy wanted a curving sidewalk made from red-clay paving brick. The sidewalk curved across the lawn and connected to the driveway about twenty feet away from the city sidewalk.
Four years earlier I had built a small brick patio and sidewalk at her mom’s home using a reclaimed thick paving brick.
I had placed that patio brick in a mixture of compacted sand and Portland cement. I just butted up the bricks next to one another and they held up remarkably well. Later I discovered the reason was the bottom of the brick bonded to the sand and cement mixture.
After searching several salvage yards, I came up empty handed not being able to find the same brick my mother-in-law had purchased. I did locate new paving brick that would work. There were two thicknesses: 2 and 3/4 inch and 1.5 inches.
The thinner brick appealed to me for any number of reasons, not the least of which it was much cheaper. I loaded up my Ford F-100 half-ton pickup with hundreds and hundreds of them until the truck springs started to complain.
It’s important to realize I was doing this job in the evenings and weekends as I was working full time doing work at other jobs. I was tired when I got home and on the weekends my mental outlook about more work was not the best.
I decided to just set the thin pavers in the sand without any Portland cement. I had read an article in some book that it would work. I could get the sidewalk done so much faster doing it this way.
Within a few weeks, the job was done and the sidewalk looked great. Kathy was very happy. So were the local ants and weeds.
Within a month, the local ant population embarked on a quest to transport the sand from under the brick creating small mountain chains on top of the sidewalk. Weeds were sprouting in nearly every crack between individual brick.
I then noticed that if you strayed to the side of the brick and stepped on the edge brick, they’d slide into the grass and tilt sideways. In other words, my shortcut sand experiment was a mistake.
The following year I ripped out all the brick, dug out the sand and more soil and poured a steel-reinforced concrete base about 5 inches thick. Using a rich mixture of Portland cement and sand, I mortared the thin paving brick on top of the concrete.
That second-generation sidewalk is still in great shape forty years later. Don’t be weak-minded like I was. Shortcuts sometimes are the longest way to your goal!
Never forget - Do It Right, Not Over!
Subscribe to the AsktheBuilder Podcast
![]() |
![]() |
|
. | ||
![]() |
![]() |