December 19, 2018 AsktheBuilder Newsletter
Are you a brand new subscriber? Welcome and thanks for your trust. Honorable subscriber of record? Thanks for remaining on the list. You're a blessing!
This is going to be a pictorial newsletter as I'm up in Bar Harbor right now getting ready for my third day of taping hours of video footage of the framing of my daughter and son-in-law's new home. I'm also taking hundreds of high-resolution photos.
Over the next few months, you're going to be treated to some tasty construction eye candy, that's for sure.
The last issue I shared a photo of the foundation and you may have been one who wondered why the house only sports a crawlspace instead of a full basement.
There are two reasons:
- ledge
- not enough fall across the lot to support foundation drain tile that would daylight
If you blast a hole in solid granite for a full basement and you can't have a trench extend to daylight where ground water would flow on its way to the ocean, then in short order you end up with a covered swimming pool instead of a bone-dry basement that would be the pride of the Atacama Desert.
If this describes your home - one that doesn't have its drain tile pop out of the ground allowing water to flow by gravity - then you must have a sump pump that does its best to keep your basement dry.
CLICK HERE NOW to get a feel for the best way to install drain tile in your home. I loath sump pumps for any number of reasons - primarily they fail when you most need them. Sump pumps with the most capacity need electricity to operate and electricity can be in short supply during horrible storms that produce vast quantities of rainwater that enter the sump.
Once your electricity goes out, your basement starts to fill with water. Too bad so sad. All that pain could be avoided by purchasing a lot that allows you to have a drain tile that extends to daylight.
Rest assured that I'll be writing many new columns about what you see in the following photos. I've already started a MASSIVE audio series featuring SHORT six-to-seven minute episodes about each step of the process. CLICK HERE to listen to these short episodes.
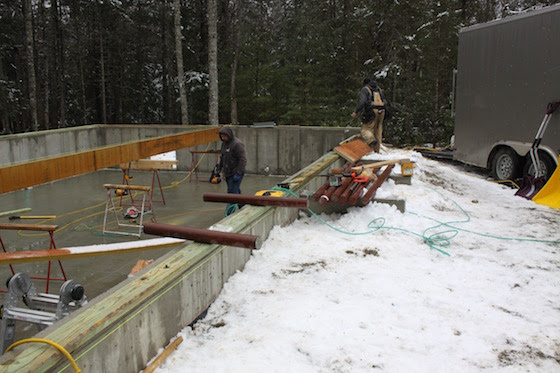
The above photo was taken about 90 minutes after the framing crew started to work on Monday morning. The first task was to shovel all the snow out of the crawlspace! Note the round steel columns, better known as lally columns, that will be used to support the massive LVL beam running the length of the house.
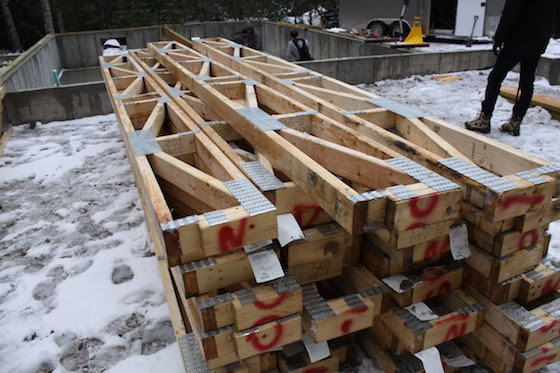
You're looking at floor trusses. These are being used instead of traditional solid floor joists.
You'll discover quite soon why I specified these in the home. These are not too tall and the reason for that is because tall floor trusses on a first floor create problems at exterior doors. Once again, I'll be explaining all this in videos, future podcasts and in articles on my website.
CLICK HERE to discover lots more about fantastic floor trusses.
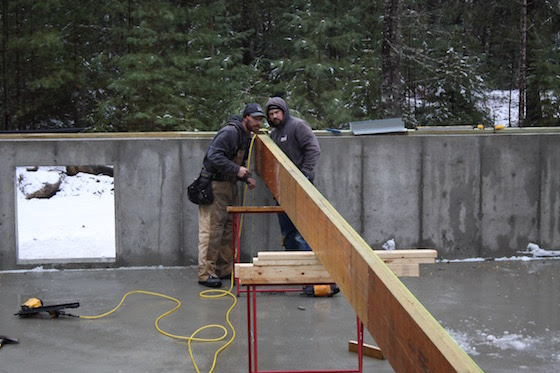
Miguel is on the left. He's the foreman of the crew. John is on the right side of the giant LVL beam. Miguel is like the Energizer Bunny.
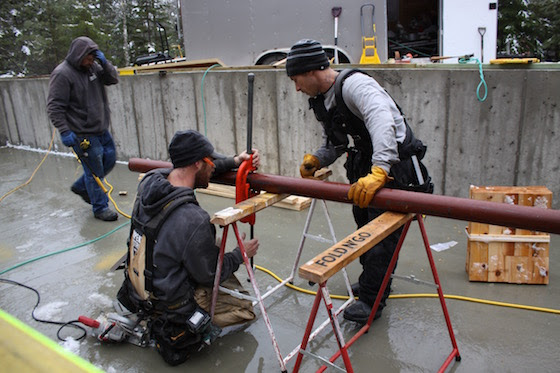
Miguel is using a special pipe cutter to cut a lally column that goes under the giant LVL beam. Pauley is helping to hold the column steady and John is pondering why he's working in the misting rain and cold. Once again, try to hold all your questions about what's going on. Believe me in upcoming newsletters, I'll explain EVERYTHING you're seeing in the photos.
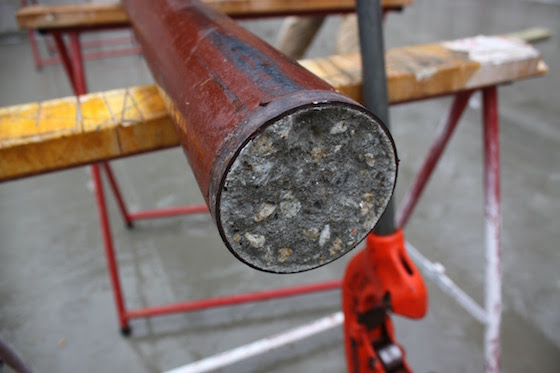
This is the end of the lally column once it's cut. Do you know what that is inside the column and more importantly, WHY it's in there? No worries - I'm going to explain all of it to you quite soon!
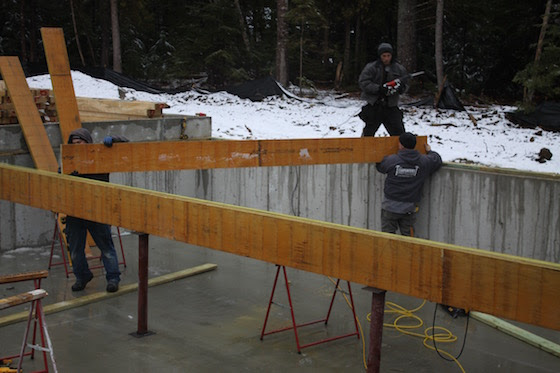
A smaller LVL beam is being placed on top of the main LVL and the foundation wall. This beam will transfer a concentrated load from the second floor floor-truss system down to the earth. It's all about continuous load pathways when it comes to structural support in your home.
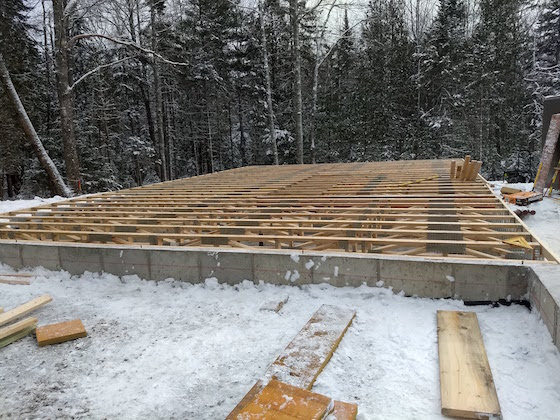
This is what the house looked like yesterday about 10:45 in the morning. The Advantech subflooring was about to be installed. That was finished by 1:00 pm.
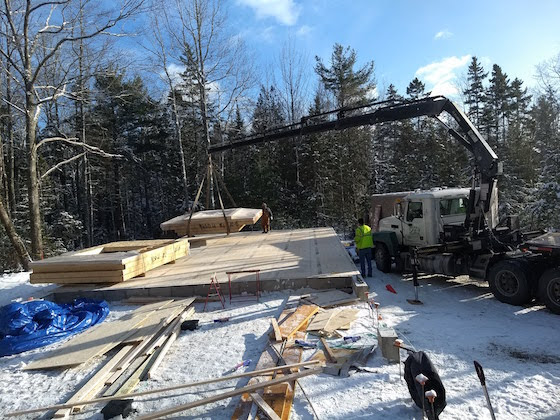
At 1:25 pm yesterday, the delivery truck started dropping off the prefabricated walls for the first floor and the garage. Yes the walls were made in a factory about 150 miles away and trucked to the site.
Factory-built wall panels allow for much greater precision. Building the walls under a giant factory roof keeps all the materials DRY.
Prefabricated walls allow the crews to shave days, and in some instances weeks, off the schedule. That's very important when building in Downeast Maine in the winter.
CLICK HERE to travel to the Structural Building Components Association Best Way to Frame website. You'll discover a treasure trove of things about floor trusses, prefabricated walls and any roof truss you might imagine.
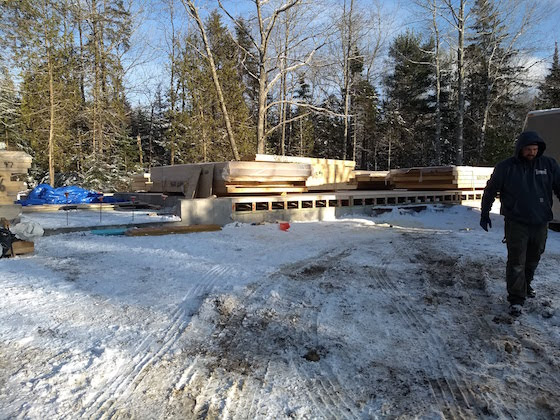
All the wall panels are stacked on the floor in pre-determined piles so there is zero wasted motion standing them up and putting them around the subfloor exactly where they belong.
I'll be leaving to go tape more video in about an hour. It's Wednesday morning about 7:09 am as I type these words.
That's enough for now. I'll be wearing my Dickies Flex coveralls today as I did yesterday. They do a superb job of keeping me warm!
Tim Carter
Founder - www.AsktheBuilder.com
Certified Organic Cleaner Man - www.StainSolver.com
Morse Mania - www.W3ATB.com
Do It Right, Not Over!