Cracked Concrete Carport & Rubbing Door
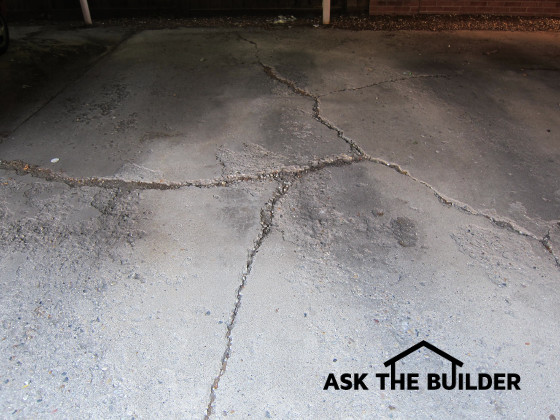
This is a cracked concrete carport slab. There’s no silver bullet to make it better other than start over. (C) Copyright 2018 Tim Carter
Cracked Concrete Carport & Rubbing Door
I’m blessed to have you as a reader and furthermore, I’m fortunate to get about 10,000 visitors a day to my AsktheBuilder.com website. Your questions are the fuel that keep this column vibrant and hopefully interesting! If you’ve got a question, then by all means visit the website and click the Ask Tim link!
Last week, I was flooded with great problems to solve. James H. lives in Evanston Illinois, in a condominium complex. The first thing to remember is not all condo complexes have garages. Some have carports that stop most sunlight, some rain, and no blowing snow.
James sent me two great photos of his crumbling and cracked concrete carport slab. It was in horrible shape. He indicated the slab could be as much as sixty years old! I must admit, it looked in sad shape.
His question was simple: “What can we do to fix this problem other than removing and replacing it, which we don’t want to do?” Having installed thousands of square feet of concrete slabs for driveways and garage floors that get car and truck traffic, I knew the answer.
The answer can be found on Meredith Center Road in Laconia, New Hampshire. It’s a long road that runs north and south along the eastern shore of Lake Winnisquam. My wife and I travel this road each Sunday on our way to and from church. It’s important to realize we have severe frost heaving issues in New Hampshire with our roads.
Three years ago, the state repaved a six-mile stretch of this road. I’m quite interested in projects like this for a host of reasons. They started the project at the south end and I happened to be on the road the day they were delivering the large machines that would do the work.
I saw a very unusual machine I’d never seen before. It turns out it was a giant, and I mean giant, grinder. This machine had the capability to chew through 12, or more, inches of asphalt paving reducing it to a mix of asphalt gravel and sand.
A few days later, I drove the road again and the machine had ground up about 2.5 miles of the roadway. A grading machine smoothed it, created a curved crown for drainage and heavy compactors packed the old ground-up pavement. For some reason, they never ground up the north 3.5 miles of the road.
A month later, they installed new blacktop on the entire road. As you can imagine, the road was smooth as silk and a pleasure to drive on.
This winter has been bitter cold and the frost heaves in the roads are the worst I’ve seen in at least seven years. The south section of Meredith Center Road still looks as good as the day they paved it. There’s not one crack anywhere or any frost damage.
The north section looks horrible. All the frost heave cracks that were there before have telegraphed through the new expensive asphalt. The gapping cracks are allowing more water to flow under the pavement which exacerbates the frost heaving.
The moral of the story is don’t expect any type of overlay on concrete to restore it to its former beauty for long. The nasty cracks will reappear. James needs to rip out the old slab. The new concrete needs to be at least 6 inches thick, it should have 1/2-inch steel bars in it both directions set at 2-foot centers. The grid should look like an empty piece of graph paper. The steel should have at least 2 inches of concrete under it.
I’d order the concrete to be 5,000 pounds-per-square-inch (PSI) strength. The minimum acceptable standard is 4,000 PSI. It costs just a little more for the extra Portland cement to get to 5,000 PSI. This new slab should look good for at least fifty, or more, years.
Dan in Boulder, CO, reached out to me with a simple problem with his bathroom door. The top right corner was sticking to the jamb when he’d try to close or open it. He was able to temporarily solve the problem by tightening the top hinge screws, but in a few weeks the door would rub again.
The solution is simple. I instructed Dan to remove the center screw in the top hinge and take it to his local small neighborhood hardware store. Once there, I told him to get the exact same screw, but be sure it was 2.5 inches long. I also told him to get a 3/16-inch wood dowel rod and a small bottle of yellow carpenter’s glue.
The next step is to open the door fairly wide and place some wood shims under the lower corner of the door directly below the handle. These shims will support the door and eliminate stress on the lower hinge as Dan starts the repair.
I told Dan to remove the other two screws on the hinge where it attaches to the door jamb and swing it out of the way. He then needed to cut two 1-inch pieces of the wood dowel rod and whittle the tip down if needed to get it to fill the holes of the top and bottom hinge screw holes. The carpenter’s glue would be used to coat the dowel and inside of the hole. Dan needed to tap the dowels into the door jamb making sure they were flush.
The next step was to flip the hinge back into position and drive the long screw he bought through the center hinge hole. I told him he’d have to drill a small pilot hole in the rough jamb as well as in the new wood dowels. The long screw would bite into the wood rough jamb behind the visible door jamb and keep the door from sagging in the future.
Column 1235